This article was published in the Spring 2010 issue of the SAQA Journal, a publication of Studio Art Quilt Associates. We're happy to support the beautiful work of art quilters through our membership, donations, writing and photography.__________________________________________________
By Alleson Kase
Photos by Ellen Agger

There’s nothing quite like the sensuous surface of hand-reeled silk. Its slubs add depth. Its sheen adds warmth. When it’s handwoven, you can see the hand of the maker in the silk, says Jamie Pratt, a quilt artist from Halifax, Nova Scotia, Canada. Add to this the subtle golden colour from coconut husks or the sky blue from the flowers of the butterfly pea and you have extraordinary fabrics – art in themselves.
When you take this fabric and transform it into a new piece of art – an art quilt – you can see the hands of many makers in the finished piece. And the making of the new form of art has a richness that goes far beyond each of those makers – a fusion of traditions and contemporary creativity, a way to weave women together.
I have admired women’s weavings since my first visit to Guatemala 30 years ago. In the intervening decades I’ve learned that handwoven cloth is an important source of income for many rural women in the developing world; a vital part of what sustains them, their families and their communities, while sustaining their cultural heritage.
Several years ago, my friend Ellen and I visited PraePan, a women’s weaving co-op in Khon Kaen, Thailand. PraePan’s members, like other women in Northeast Thailand and much of Laos, weave in their homes on foot-treadle floor looms made from hardwood and bamboo. Without metal heddles, the warp yarns are usually raised with patterning strings and/or bamboo strips. The weft yarns are thrown by hand in a slender "boat" shuttle, carved from local hardwood, stained dark and worn smooth by years of use.

Before warps are strung or bobbins filled, women spend months preparing the yarns. Many raise silkworms, boil cocoons and reel silk threads. Some spin their own cotton, after removing the seeds and fluffing the boll into a cloud of fiber. Almost all dye their own yarns, using natural materials they have grown or gathered close to their homes.
The women distill a wonderful array of nature’s colors from leaves, husks, wood chips, barks, berries, fruits and flowers. Slate blues, peony pinks, herbal greens, and spicy browns: all their colors seem to have a third dimension not captured on a color chart and rarely duplicated.
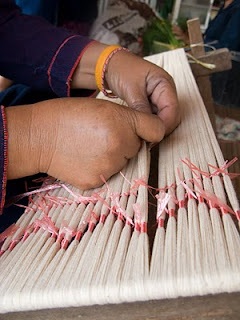
Many tie-dye the yarns before weaving with a traditional technique that they call "
mudmee," and which we in the West usually refer to as
ikat. [Described in a travelogue by Karen Maru in SAQA Journal, Spring 2008] When the
mudmee yarns are woven, an elaborate geometric pattern emerges and repeats. If the artist is especially expert, as well as diligent, the pattern can continue for 20 meters!
During a village visit, we saw that their artistry is matched by their practicality. They have adopted fuel efficient stoves for their dye pots, and abandoned heavy metal mordants that pollute village streams. Membership in the co-op gives women access to trainings and appropriate technologies from local rural development groups. These let them improve their products and decrease their costs, while they protect their health and the health of their communities.
Members sell their weaving to the group, receiving payment when pieces are finished rather than when they’re sold to a customer. During our first visit, however, we learned that PraePan had been forced to decline recent requests for new membership because their members were already creating more products than the co-op was selling. On the spot, we decided to buy a portion of the group’s inventory to bring home to Nova Scotia, Canada.
Weaving international links We realized that a one-time purchase was not going to address PraePan’s marketing problem, so the next year we returned to discuss possible strategies that might lead to a long-term increase in sales. Our first suggestion was to connect them to the Internet, as well as develop a website and shopping cart for them. In dialogue with PraePan staff, we came to understand how impractical this was: the women do not read or write English, so they could not respond to email enquiries that a website would generate.
More crucial is the fact that there are more than 70 million web sites and millions of online shopping carts. Customers must be driven to web sites; given the competitive nature of online marketing, they must also be convinced that artistry, fair trade and environmental stewardship override other concerns of price, availability, and selection. This task is a formidable one that would leave weavers no time to weave, even if they had the skill and resources to take it on.

Consequently, we formed a social enterprise to market their artwork. We call it TAMMACHAT, which is Thai for "natural." Each year we travel to Thailand and Laos to visit PraePan and other similar groups of village weavers who we meet through their networks. We support these artisans and their communities by choosing quality pieces that are produced with environmentally and socially sustainable practices, by paying fair prices set by the artisan groups themselves, and by returning to the same groups each year with the intent of increasing their income stability through long-term trading relationships.
Some of our customers care about these factors as much as we do; others only need to see the unique beauty of the textiles to appreciate them. Either way, the makers and their methods of production are supported and encouraged. Fiber artists of all sorts seem the most appreciative of our message and these products. Who would better understand the intricate ways that fibers weave us all together?
Un-natural fibersSilk, cotton and bamboo are all "natural fibers" but they are seldom produced naturally. Most silk is produced in factories that rely on heavy doses of toxic sanitizers and, consequently, are unhealthy workplaces. [See footnote 1 at end of this blog post.] Most cotton is grown with large inputs of chemical fertilizers, insecticides, herbicides, and unsustainable quantities of irrigation, so much so that an entire sea has been drained dry to produce "affordable" cotton clothing. ["Disappearance of the Aral Sea," Journal of Soil and Water Conservation, May 01, 2006.] Bamboo, the latest green-washed fiber, grows quickly and naturally in the wild but is an extruded yarn produced by an industrial chemical process with toxic effluents like most other
rayon.
The weaving groups we work with create silk fabrics that are 100% organic: the silk they weave is raised and reeled in villages; the mulberry leaves fed to the silkworms are free from pesticides; their remarkably dynamic colors are created with natural dyes that are wild crafted or organically raised.

These weavers live in areas too dry to support cotton production without irrigation, which they don’t have. This means that, while they do their own dyeing, they usually purchase their cotton yarns. On the other hand, we spent two weeks last year with a group that grows heritage varieties of cotton on the banks of the Mekong River without toxic chemicals or unsustainable irrigation. Together we designed two indigo cotton jackets and a line of decorative pillows. This year we will return there, as well as look for more organic cotton production on the Lao side of the Mekong.
Joint projectsBecause quilting is not a traditional style of handwork in this part of Thailand, we initially had some trouble explaining to Thai weavers how their silks might be used by fiber artists in the West. Knowing that a "picture is worth a thousand words," we went online with the technology of a cell phone and a laptop computer to introduce staff members of another weaving co-op, PanMai, to the artwork of
Laurie Swim and
Valerie Hearder – women we know in Nova Scotia who are also internationally known quilt artists, authors, and instructors.
With that shared understanding, and the weavers’ help and artistic advice, we have produced a unique line of silk squares in four different palettes -- each package containing one
mudmee design and four solid colors. We’d gotten the initial idea from Val Hearder, who suggested that we might want to bring silk squares to the bi‑annual Quilt Canada conference. Three months later, we did just that and found that Val was right.
During our next visit, we will discuss with these groups the growing demand in the West for ethically-sourced clothing and share the good news that their extraordinary silk scarves and fabrics are now eco-fashionable.
We hope that increased public awareness of the impacts that textile production has on people and the planet will prompt people to embrace these "slow fashions" as they have "slow food." We hope that groups like PraePan and Panmai can hang on a little longer while the world catches up to their traditional ways, so that they can better sustain what they have learned from their grandmothers and are now preserving for their granddaughters.
__________________________________________________
Alleson Kase and Ellen Agger live most of the year in Nova Scotia, Canada. Together they have created TAMMACHAT Natural Textiles, a social enterprise that imports handwoven silks and cottons from Thailand and Laos. They market these at fair trade textile events that they create, as well as online at
www.tammachat.com.
~~~~~~~~~~~~~
Footnote:
1. Chlorine, formalin, lime and anti-fungus drugs are used to reduce disease among intensively raised hybrid silkworms. Many women find that they are allergic, or worse, to these chemicals. Symptoms include headaches, eye pain, nausea, vomiting, fatigue, fainting, dyspnoea, coughing, numbness, skin rashes, itching and eye swelling. From “
Gender and Natural Resource Management: Livelihoods, Mobility and Interventions.”